In der Montage entstehen aus Hunderten von Einzelteilen BMW und MINI Hochleistungsmotoren nach Kundenwunsch. Dabei ergänzen sich modernste Produktionstechnologien auf perfekte Weise mit dem Know-how und dem Geschick qualifizierter Montagearbeiter.
TAKTANGEBEND.
Die Motorenmontage.
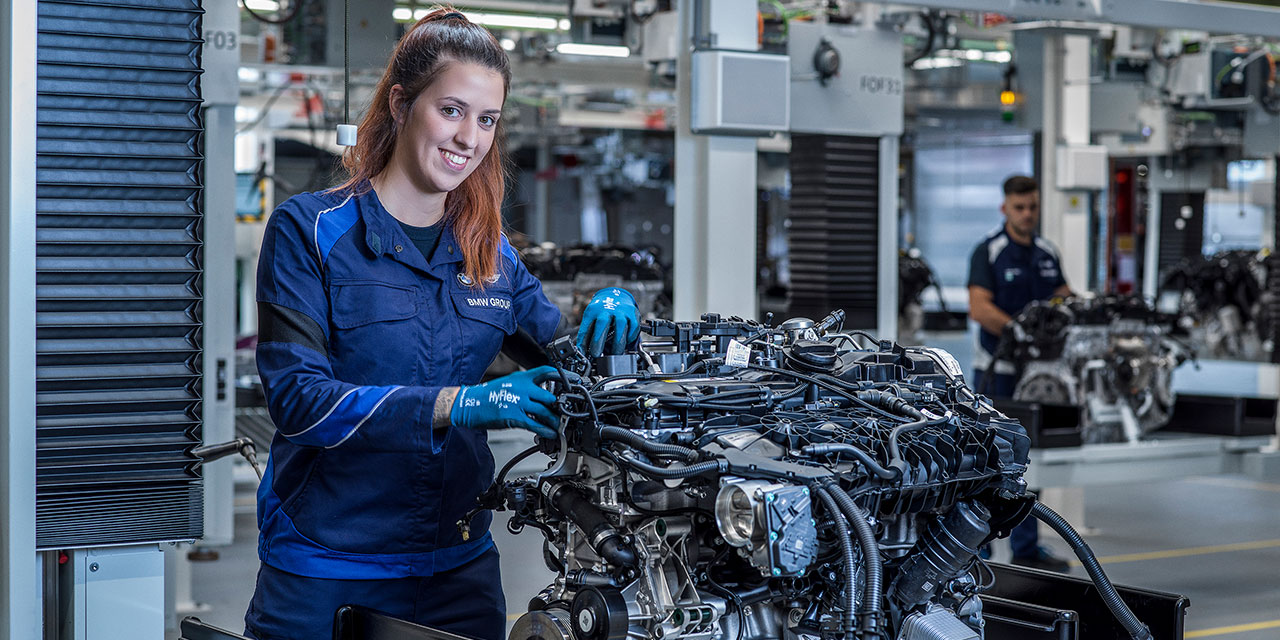
Unzählige Motorvarianten.
Alles beginnt mit dem Zusammenbau des Grundmotors. In weiterer Folge werden die Kernteile zusammen mit weiteren Komponenten zum sogenannte Rumpfmotor aufgebaut – Schritt für Schritt wird der Motor dann komplettiert. Spannend wird es, da bei uns hunderte verschiedene Motorvarianten über die Montagebänder laufen. Da aber unsere Mitarbeiter absolute Könner ihres Fachs sind, beherrschen sie die hochkomplexe Variantenvielfalt. Unterstützt werden sie dabei durch modernste Produktionsprozesse, einen hohen Grad an Digitalisierung, Logistik am Puls der Zeit und ein innovatives Baukastensystem mit Engine Sets für die Motorenmontage.
Umweltschonender Kalttest.
Jeder fertiggestellte Motor absolviert schlussendlich einen Funktionsprüflauf, den sogenannten Kalttest, der computergesteuert überwacht wird. Dieses Verfahren ist besonders umweltschonend, da der Motor ohne Kraftstoff über einen E-Motor betrieben wird. Danach treten die Motoren ihre Reise in die Fahrzeugwerke zur sogenannten „Hochzeit“ an – dem Zusammenbau von Motor, Fahrwerk und Karosserie.
Bewegt revolutionär: Baukastenmotoren.
Basierend auf einem einheitlichen Konstruktionsprinzip mit Reihenanordnung, lassen sich zukünftig an einem Montageband bis zu vier Grundmotoren herstellen – daraus lassen sich wiederum Länder- und Leistungsabwandlungen ableiten.
Ergonomische Arbeitsplätze.
Höhenverstellbare, elektrische Hängebahnen sorgen entlang der Montagelinien dafür, dass Mitarbeiter von unterschiedlicher Körpergröße ergonomisch optimal arbeiten können. Damit wird ein wichtiger Beitrag zur Gesundheit und Leistungsfähigkeit der Mitarbeiter geleistet.